【协会四十周年】焊接技术撑起中国尊的新高度
编者按
中国工程建设焊接协会自1984年成立以来,已经走过了充满挑战和收获的四十年。工程建设行业作为国家发展的重要基石,其质量与技术水平直接关系着国家的未来与人民的福祉,焊接技术作为一项基础且关键的工艺,对于保障工程结构的牢固性、可靠性和耐久性扮演着至关重要的角色。四十年岁月如歌,四十载征程如虹。中国工程建设焊接协会作为全国性专业协会,在引领技术进步、培养专业人才、提高工程质量和提升行业标准等方面做了大量工作,促进了国家建设和发展。四十年来,焊接界各方同仁在祖国大地上,创建了鸟巢、港珠澳大桥等一座座具有里程碑意义的优秀焊接工程和建构筑物,涌现出一大批优秀科技工作者和大国工匠等焊接界的榜样人物,在长期实践中,培育形成了“尊重科学,遵守规范;埋头苦干,道道把关;勇于创新,甘于奉献”的焊接人精神。这些精神生动诠释了社会主义核心价值观,是焊接界的宝贵精神财富和强大精神力量。
为庆祝中国工程建设焊接协会成立40周年,我们在此将陆续登载一批榜样人物的先进事迹和典型工程的诞生经历,在业内进一步弘扬科学家精神,劳动、劳模和工匠精神及焊接人精神,以这些时代楷模和行业先锋作为学习榜样,推动工程建设领域高质量发展,为加快实现中国式现代化贡献力量。
本期向大家介绍的是北京市第一高楼、首都新地标、北京中国尊大厦工程。该项目施工总承包单位为中国建筑股份有限公司/中建三局集团有限公司(联合体),其钢结构施工任务由中建钢构股份有限公司承担,焊接技术在整个建筑中发挥了关键作用,取得多项骄人的成绩。该项目荣获2018年创建“中国工程建设焊接协会优秀焊接工程”活动成果评价特等奖。
北京中国尊大厦,位于北京商务中心区(CBD)核心区Z15地块,东至金和东路,南至规划绿地,西至金和路,北至光华路。建筑高度528m,为中信和业投资有限公司投资建设,北京市第一高楼,首都新地标,世界上第一个在抗震设防烈度8度区建造的500m以上超高层大楼。该项目用地面积11478㎡,总建筑面积43.7万㎡,其中地上35万㎡,地下8.7万㎡,建筑层数地上108层、地下7层(不含夹层),可容纳1.2万人办公,为中信集团总部大楼。施工总承包单位为中国建筑股份有限公司/中建三局集团有限公司(联合体)。中建钢构股份有限公司承担其钢结构施工任务,焊接技术在整个建筑中发挥了关键作用,取得多项骄人的成绩, 1项国家十二五重点课题;1项国家级工法,2项省部级工法、15篇核心期刊论文;10项发明专利、8项实用专利3项省部级进步奖4项技术鉴定;(3项国际领先,1项国际先进)。该项目荣获2018年创建“中国工程建设焊接协会优秀焊接工程”活动成果评价特等奖。QC管理成果获得公司级奖项5项,省市级奖项3项,国家级奖项4项;中建总公司QC成果一等奖,获得北京市QC成果一等奖,中国施工企业管理协会、中国建筑业协会QC成果一等奖;获得结构“长城杯”金奖。项目参编《多腔钢管钢筋混凝土结构技术规程》。
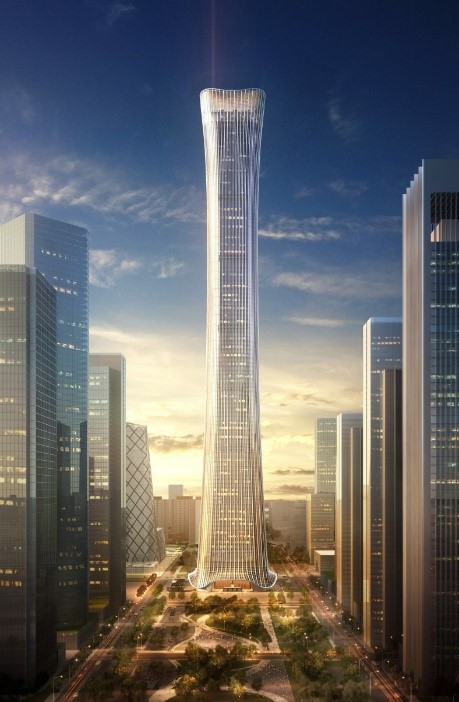
造型独特新颖,超高层建筑的典范
大厦采用巨形框架(巨柱、转换桁架、巨型斜撑组成)+混凝土核心筒(型钢柱、钢板剪力墙)结构体系。F105层以上为塔冠结构,向上延伸至屋顶,其高度为30.3m,造型独特新颖。主塔楼为筒中筒结构,内部为型钢混凝土核心筒,外筒由巨型支撑和巨型框架以及次框架组成。内外筒共同构成多道设防的抗侧力结构体系。
核心筒从承台面向上延伸至大厦顶层,贯穿建筑物全高,核心筒平面基本呈正方形,底部尺寸约为39m×39m。核心筒周边墙体厚度由1200mm从下至上逐步均匀收进至顶部400mm;筒内主要墙体厚度则由500mm逐渐内收至400mm。核心筒采用内含钢骨(钢板)的型钢混凝土剪力墙结构,在结构底部范围墙肢内设置了钢板,形成了组合钢板剪力墙。在塔楼腰部区域核心筒周边墙肢内均匀布置了型钢暗撑。通过设置钢板墙和钢暗撑,有效地减轻结构自重。外筒由巨型柱、巨型支撑、转换桁架以及次框架组成的巨型框架筒体结构。巨型柱位于建筑平面四角并贯通至结构顶部,在各区段分别与转换桁架(腰桁架)、巨型支撑连接。巨型柱平面轮廓为矩形,沿建筑高度向上尺寸逐渐缩小。巨型柱采用钢管混凝土柱。巨型支撑设置在结构四边的垂直立面上,采用焊接箱型截面,并与巨型柱连接。转换桁架(腰桁架)沿塔楼竖向建筑功能节间布置,连同顶部的冒桁架,共8道,配合转换桁架所在楼层四角设置角部桁架,形成环状稳定结构。
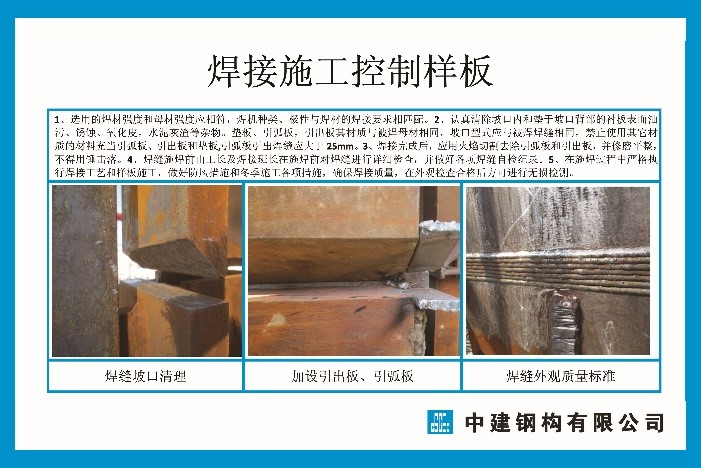
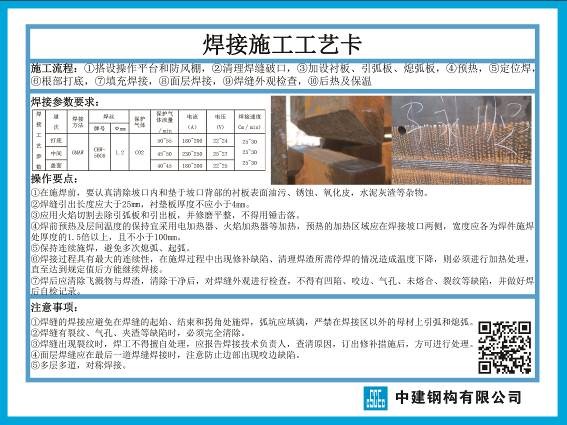
攻克焊接关键,解决施工难点
多腔体异形巨柱焊接变形控制及应力释放。大厦项目采用巨型框架加型钢混凝土核心筒的框筒结构形式,位于建筑物平面四角的异型多腔体巨柱为此体系的主要传力构件。其底部截面面积约63.9㎡,钢板厚度最大为60mm,材质主要为Q390GJC、Q345C,由4个构件平面组装而成,分为13个腔体,巨柱底面截面尺寸和腔体数量均未世界之最。焊接作为巨柱之间连接形式,焊接变形的存在影响着构件的强度、刚度以及稳定性,能否有效降低焊接变形直接影响到现场安装精度和工期节点。如何采取合理的焊接顺序、减少焊接残余应力的产生,确保现场焊接质量是焊接施工的一大难点。
巨型转换桁架高空原位拼装及密集焊缝焊接。工程转换桁架焊缝存在大量50mm、60mm厚板,焊接工作量大、难度高,且主要为横焊缝、平焊缝、仰焊缝及立焊缝,处于超高空、悬挑临边部位,单侧大截面尺寸焊接节点数量达44处,焊缝密集、焊接作业条件十分复杂,作业时需搭设焊接操作平台,防风、防雨、确保安全的措施非常规工程可比;桁架上下弦对应巨柱多腔体,存在局部腔体尺寸狭小,焊接条件较差,施焊难度较大;转换桁架施工跨越冬期,期间最低温度可达-15℃,海拔高度每升高100m,气温下降0.6~1.0℃,外界环境条件较差,需做好焊前预热焊后保温。如何采取有效措施控制焊接变形、消除残余应力、防止层状撕裂是现场焊接施工一大难点。控制超长超厚钢板墙焊接变形。钢板墙水平焊缝最大长度6.4m,竖向焊缝最大长度4.5m,超长焊缝焊接难度大。最大板厚为60mm,厚板焊接变形及残余应力控制是关键。且冬季施工焊接质量控制难。制定严密的焊接工艺流程,开展焊接工艺评定。根据《钢结构焊接规范》(GB50661-2011)规定,表6.2.4评定合格的试件厚度与工程适用厚度范围,厚度小于25mm的试件钢板适用于3mm~2t的钢板,厚度25<t≤70试件板厚适用于板厚mm(0.75t~2t)的钢板。本工程所使用钢板材质为Q345B、Q345C、 Q345GJC,和Q390GJC、Q390GJD(巨柱加强区面板及竖向分腔板),其中Q345B、Q345C, Q345GJC属于Ⅱ类钢材,Q390GJC、Q390GJD属于Ⅲ类钢材,根据钢结构焊接规范要求,Ⅱ、Ⅲ类别钢材中高级钢材的焊接工艺评定结果可代替低级别钢材,因此本工程选用Q345GJC钢材做Ⅱ类钢材焊接工艺评定,可代替Q345B、Q345C钢材材质,选用Q390GJD钢材做Ⅲ类钢材焊接工艺评定。
现场安装焊接工艺评定项目选用安装焊接工程中,最具典型的构件板厚规格、焊接位置和构件材质的焊接接点,同时根据工期计划,考虑冬季施工部位,使用焊接评定试件必需与工程所用钢材的材质相同。本焊接工艺评定选用25mm厚钢板和30mm厚钢板进行试验。根据钢结构现场负温度(焊接温度低于-10℃)条件下安装焊接施工特点,对现场采用的钢材、焊接材料、焊接方法、接头形式、焊接位置、焊后热处理制度以及焊接工艺参数、预热和后热措施等各种参数的组合条件进行焊接评定实验。
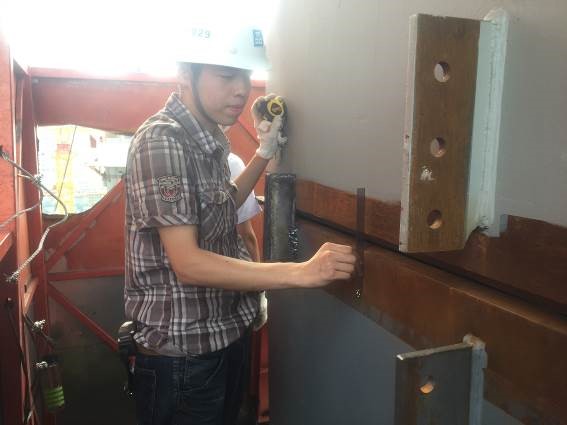
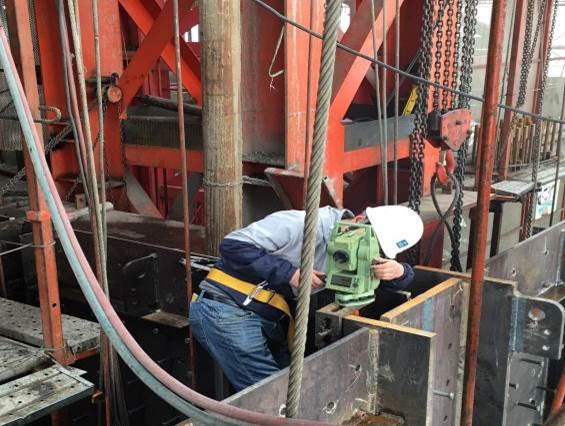
全过程、可追溯焊接质量控制
本工程主要钢构件材质为Q345B、Q345C、Q345GJC、Q390GJC,焊接方式有手工电弧焊和二氧化碳气体保护焊。为保证焊接质量,加强全过程焊接质量控制。焊前准备,对进场的焊机设备进行调试,保证机具使用要求。焊材准备,现场焊丝取样复试。样板引路,在现场焊接操作区域挂设工艺牌及施工样板,下方附带二维码,扫描后链接到焊接专项施工方案,使得现场各焊接小班组对工序施工要点、关键控制点、质量保证措施等更加熟悉,确保了对焊接施工质量做到了事前控制、统一标准,有利确保了后续焊接工序施工质量。根据《钢结构工程施工质量验收规范》GB50205-2001 和《钢结构焊接规范》GB50661一2011 第六章“焊接工艺评定”的具体条文进行。结合工程的结构特点、节点形式等编制焊接工艺评定试验方案,经业主或监理认可后实施。焊接工艺评定需邀请业主、顾问和监理参加。焊接完毕后对试样进行标识、封存运送到检测单位。技术员根据现场记录参数、检测报告确定出最佳焊接工艺参数,整理编制完整的《焊接工艺评定报告》并报有关部门审批认可。《焊接工艺评定报告》批准后,技术员再根据焊接工艺报告结果制定详细的工艺流程、工艺措施、施工要点等编制成《焊接作业指导书》用于指导现场的焊接作业。
正式施焊前还要将《焊接作业指导书》细化,并对现场施焊人员进行焊接施工技术专项交底。焊接过程控制。焊接防护。焊接施工时,为了保证焊接作业在良好的作业环境下进行,项目部在焊接施工部位搭设焊接防护棚,要求防护棚:上部稍透风、但不渗漏,兼具防一般物体打击的功能。中部宽松,能抵抗强风的倾覆,不致使大股冷空气透入。下部承载力足够4名以上作业人员同时进行相关作业,需稳定、无晃动;可以存放必需的作业器具和预备材料且不给作业造成障碍,无可使器具材料脱控坠落的缝隙,下部防护采用阻燃材料遮蔽。焊前检查。现场焊接施工前,由项目测量工长对安装精度进行检查,合格后通知质检人员检查焊接部位,检查焊口部位的组装和表面清理的质量,要求坡口内和垫于坡口背部的衬板表面无油污、锈蚀、氧化皮,水泥灰渣等杂物;检查引弧板,引出板和钢衬垫板的加设是否满足方案及相关规范要求;验收合格满足要求后,再通知焊工班组长安排人员施焊。焊前预热。为保证焊接的质量,减小焊接应力的产生,预热及层间温度的保持采用电加热器、火焰加热器等方式进行,并使用专用的红外测温仪器检查。预热的加热区域应在焊接坡口两侧,宽度应各为焊件施焊处厚度的1.5倍以上,且不小于100mm,预热温度宜在焊件反面测量,测温点应在离电弧经过前的焊接点各方向不小于75mm,当用火焰加热器预热时正面测温应在加热停止后进行。焊口预热(电加热板)。层温检查,与预热一样,焊缝层温控制十分困难,焊接时焊缝焊接的长度,应控制在一定长度1m左右,需随时对焊接焊缝进行测温监控,层间温度应控制在不低于预热时的温度(即层间温度应不低于120℃),发现层温过低时,必须立即进行加热补偿,待达到温度后再进行焊接。单节点焊缝连续焊接完成,不允许无故停焊,层间温度过低或超高时,立即采取补热、停焊的方法,待层间温度达到施焊条件后再进行焊缝焊接。如遇特殊情况中途必须停止焊接,立即对焊缝进行保温处理,当焊缝再次焊接时需重新对焊缝进行加热,加热温度比焊前预热温度相应提高20~30℃。焊后保温。现场焊缝焊接完成后,后使用电加热设备将焊缝两侧200mm范围内加热至200℃ ~250℃,保持温度70min~120min,过程中实时对温度进行监控。焊缝外观检查。当焊缝温度经24h至常温后,采用目测法观察焊缝外观。焊缝表面缺陷超过质量标准时,对气孔、夹渣、焊瘤、余高过大等缺陷采用砂轮打磨,对焊缝尺寸不足、咬边、弧坑未满等缺陷进行现场补焊。焊缝无损检测。外观检查合格后,对母材两侧打磨至见金属光泽进行无损探伤,自检由北京市建设工程质量第三检测所进行100%检测,自检合格由第三方(中冶建筑研究总院有限公司建筑工程检测中心)进行抽检。焊缝打磨。隐蔽焊缝无损检测,焊缝自检探伤,三检探伤。
根据本工程结构特点,焊接时采取整体对称焊接与单根构件对接焊相结合的方式进行,焊接过程中要始终进行结构标高、水平度、垂直度的监控。(1)结构对称、节点对称、全方位对称焊接。(2)由于节点焊缝超长、超厚,施工过程需在临时连接板上根据要求增加拘束板进行刚性固定,控制焊接变形。(3)焊接节点采取分段、对称的焊接方法,钢板墙采用先立后横的焊接顺序,巨柱焊接先焊接对构件整体变形影响较小的焊缝,按照本方案巨柱焊接顺序焊接。(4)焊缝采取窄道、薄层、多道的焊接方法。(5)为保证钢柱的精度,采用先内后外,先柱后梁,再斜撑,先焊收缩量大的再焊收缩量小的焊接方法,待全部钢柱完成焊接后,再进行梁的焊接,为保证焊接后结构的整体精度,从结构面的中部开始梁的焊接,尽可能减少焊接应力,待内筒全部完成焊接后,再进行外筒柱、梁、斜撑的焊接。(6)施工中柱与柱、梁与梁、梁与柱、斜撑的施焊,制定严格规则遵循执行。
核心筒焊接主要坚持由内到外的焊接原则,将核心筒分为四个区域,钢梁焊接时,对于一根钢梁不能同时对其两侧焊接,应在一端焊接完成后,待达到常温后,再进行另一端焊接。
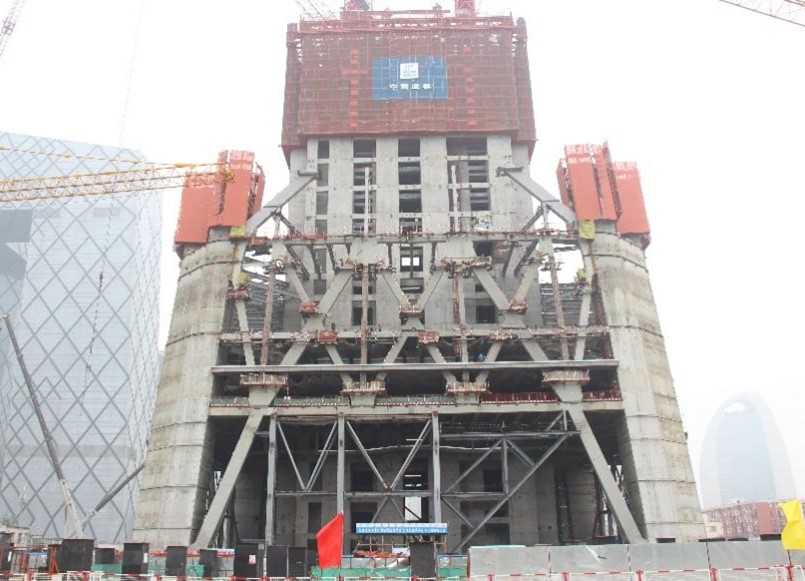
TT1桁架施工形象
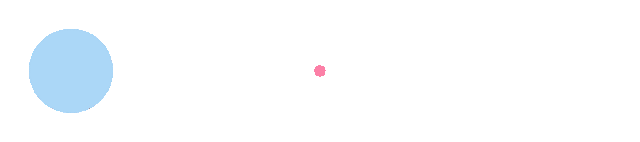
采用焊接新技术,深化设计理念
本工程厚板较多,巨型柱、转换桁架、巨型斜撑以及F25层以下核心筒钢板剪力墙使用钢板厚度均为60mm,尤其F07层以下巨型柱分段制作“工”型构件,小角度焊缝破口尺寸的控制。高强度超厚板碳当量高,淬硬倾向较为严重,对冷裂纹尤其是延迟裂纹较为敏感,焊接性较差,特别在边缘位置两侧板与中间板焊接时容易产生裂纹,深化设计时应从构造上加以合理处理(满足建筑外观要求的前提下),在深化设计阶段从构造上尽量避免层状撕裂的发生。对工艺隔板等措施的考虑本工程巨柱、巨型斜撑等构件体量大,板幅大,制作时变形较大,所以在制作过程中需设置合理的工艺隔板,以防止构件在组装、吊运过程中发生变形,同时设置合理的工艺衬板等以保证焊接质量。
防止厚板层状撕裂的构造处理。本工程厚板碳当量高,淬硬倾向较为严重,对冷裂纹尤其是延迟裂纹较为敏感,焊接性较差,特别在边缘位置两侧板与中间板焊接时容易产生裂纹,深化设计时应从构造、剖口的形状和方向加以合理处理(满足建筑外观要求的前提下),在深化设计阶段从构造上尽量避免层状撕裂的发生,为厚板焊接创建有利条件。开展巨型柱组拼工艺及焊接顺序研究。大厦项目采用巨型框架加型钢混凝土核心筒的框筒结构形式,位于建筑物平面四角的异型多腔体巨柱为此体系的主要传力构件。其底部截面面积约63.9平米,钢板厚度最大为60mm,材质主要为Q390GJC、Q345C,由4个构件平面组装而成,分为13个腔体,巨柱底面截面尺寸和腔体数量均未世界之最。焊接作为巨柱之间连接形式,焊接变形的存在影响着构件的强度、刚度以及稳定性,能否有效降低焊接变形直接影响到现场安装精度和工期节点。工程采用:“总体施工方案的编制→巨型构件焊接过程数值模拟→确定初步焊接顺序及节点形式→现场焊接应力及焊接变形监测→根据监测结果对比数值模型→调整模型参数再次进行模拟→调整焊接顺序,始终以控制焊接应力及变形为目的→得出最优焊接顺序及工艺参数”的方法,对巨型柱组拼焊接顺序和工艺进行研究,确保现场施工质量。采取多腔体巨柱分段分节方案,主要原则如下:a、要保证单体散件的重量和外形尺寸满足运输条件要求;b、满足现场吊机起重性能、且便于安装;c、满足技术规范要求、设计要求,同时避免焊接收缩及变形等要求。在进行巨型柱分段分节时,充分考虑巨型柱分段分节的保证措施。主要有如下几个方面:a)进行三维实体建模,结合塔吊布置及起重性能进行分段分节复核;b)针对复杂构件及节点进行有限元分析,使分段点尽量避开焊接应力较大且集中的位置,同时对分段分节后施工阶段结构的稳定性进行施工模拟分析;c)组织专家研讨会和论证会,针对复杂构件的分段分节进行专项研究讨论,确保构件分段分节合理可靠;d)分段后的巨柱,应该满足现场最大吊重限制。塔楼地上外框巨型柱分段分为三种方式:a) F001~F007层为六边形多腔体巨型柱,为满足构件运输和现场吊装作业要求,在横向分段后,应在平面进行再次分段。b)F007~F062层巨柱截面尺寸>3500×3500mm,均采用横向分段,分段高度≤3500mm。c)F063层以上巨柱截面尺寸<3500mm,采用按层高横向分段,且构件重量<50t。
多腔体巨柱组拼的焊接采取整体对称焊接与单根构件对接焊相结合的方式进行,焊接过程中始终进行结构标高、水平度、垂直度的监控。a)结构对称、节点对称、全方位对称焊接。b)由于节点焊缝超长、超厚,施工过程需在临时连接板上根据要求增加拘束板进行刚性固定,控制焊接变形。c)焊接节点采取分段、对称的焊接方法,巨柱焊接先焊接对构件整体变形影响较小的焊缝,按照本方案巨柱焊接顺序焊接。d)焊缝采取窄道、薄层、多道的焊接方法。e)为保证钢柱的精度,采用先内后外,先柱后梁,再斜撑,先焊收缩量大的再焊收缩量小的焊接方法,待全部钢柱完成焊接后,再进行梁的焊接,为保证焊接后结构的整体精度,从结构面的中部开始梁的焊接,尽可能减少焊接应力,待内筒全部完成焊接后,再进行外筒柱、梁、斜撑的焊接。
控制多腔体巨柱焊接应力。为了控制焊接应力,针对本工程焊接节点的特点,通过从内向外、从上到下、先焊收缩量较大节点,后焊收缩量较小节点,先单独后整体的合理焊接顺序。使焊接应力得以有效的散失,从根本上减少焊接层状撕裂源。对箱形、工字形梁柱焊接时,采取由两名作业习惯相近的焊接技工,同时、对称、匀速焊接,并尽量保持连续施焊,尽量减少碳弧气刨的使用,并再使用后用角向磨光机磨去刨削部位表面附着的高碳晶粒,以免层状撕裂的产生。尽量控制焊缝表面的余高,减少应力集中,所有焊缝余高应控制在0.5~3mm以内。工程异形多腔体巨柱是由4个Q390GJC的构件组成,共13个腔体,坡口形式有三种,两种对接接口以及一种角接接口。
根据巨柱实际接口形式,利用VISUAL-MESH建立三种局部3D实体网格模型,分别为板厚50mm的角接、板厚50mm的对接和板厚30mm的对接。
经过改变焊接顺序降低了焊接变形,立焊缝焊接时母板被约束,解决了田字形腔体向内收缩的问题,满足规范对错边要求。并且焊接变形最大值有明显降低,模拟值为20.743mm,实测值为16mm。结合现场测得数据得知此种焊接顺序有效的解决了现场安装精度问题。优化后避免了田字型腔体的焊后矫正。节省了工期,是一种高精度、高效率的施工方法。
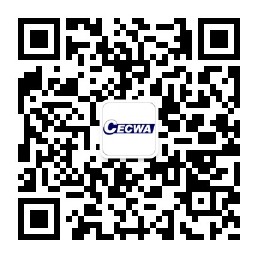